If a technician fails one or two welds, they can take a make-up test, but if they fail the make-up, they then must take the entire test over again. Failing can get very expensive.
Most OEMs sell their propitiatory aluminum coupons and provide information on what type and size of sheet aluminum to purchase for practice if a shop is part of the certif ed program. There is no training at the test, as you are expected to know how to weld prior to attending the testing.
Other required training is OEM training on specif c vehicles. Hands-on training can be two to five days depending on the OEM and how many vehicles are covered. Some OEMs have model-specific training, while others cover multiple aluminum models in an extended program. Most require ASE certif cation and I-CAR training as part of the standard requirement to be on the program. Costs can be yearly fees of $1,000 to $7,500. Hands-on training classes range from $125 to $3,500 and can take eight to 40 hours. Welding certification ranges from $800 to $15,500 and can take six hours to 80 hours for initial testing. Let's look at some examples of how the OEM programs differ:
- Audi A8, TT and R8: Hands-on class for the three models is 40 hours (five days) for the initial training and each individual model update class is
two days. The aluminum welding certification initial test for the three vehicles is 40 hours (five days) and recertification is every two years and requires four days to complete.
- Mercedes-Benz: For all their vehicles - aluminum and steel - there is a one-day, self-study online course followed by two days of hands-on training.
The aluminum welding certif cation initial test is 80 hours (10 days) and recertif cation is every six months for two days and every two-year recertification is three days.
- Ford F-150: Ford requires an eighthour classroom class administered by I-CAR and the welding certification test is also administered by I-CAR; it is an eight-hour test. Recertification is required every two years and takes six hours.
|
Each manufacturer has their own requirements, and this will continue as the new advanced substrate models are introduced each year. As an industry we must get on board - we need to get proper training and purchase the proper equipment. Training is expensive - program fees, tools and equipment, travel, lodging, meals, rental cars, a tech’s salary during training and the loss in production while the technician is away all add up. But the cost to your shop if your employees are not properly trained and equipped for the vehicles to come may be unsurmountable.
|
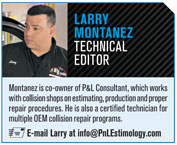 |
|